- For example, a computer is exploded into hard drives, RAM, Processors, chips etc.. which are included into the requirement of entire computer.
- The Manufacturing bill of materials(BOM) be made up of all the assemblies and parts required to construct a finished and shippable product.
Advanced Bill Of Materials (BOM):
- In latest versions of netsuite, it release a fresh features & existing functionalities.
- The Advanced BOM record is available as of NetSuite 17.2.
Enable the Advanced BOM feature in Netsuite:
- Go to Setup > Company > Enable Features
- Go to Inventory & Items tab
- Check the Advance Bill of Materials box.
Advance BOM Features:
- Allowing multiple BOM’s for a single assembly item and for a single BOM is used with multiple assembly items.
- After enable the advance BOM feature in netsuite, existing Bill Of Materials is automatically converted to read only BOM record.
- The components subtab on the item record replace by the new Bill Of Materials Subtab.
- It specify default BOM by location (previously, the same BOM was used to all locations)
- Create multiple revisions of a BOM with different effective start and end dates
- Ability to view full history of BOM revisions and effective start/end dates.
- You have to define component yield level on the BOM revision record.
Creating BOM:
There are 3 ways to create the Bill of Materials.
- Creating a new BOM record.
- Create BOM an Assembly item.
- Copying a BOM
Creating a new BOM record:
- Go to Lists > Supply Chain > Bills Of Materials > New
- In the name field enter a BOM name.
- If you apply Component yield to all BOM revisions check the box.
- Component yield preference: It is used to automatically calculate the quantity for loss of raw materials during the process. For example, you sell one assembly item (ex: Table) it made up of some components (ex: 4 legs, rod etc..). Every 100 assembly items, 10 legs are defective. When you order the “Table” to get 100 tables but you need to order 110.
- To use all assemblies in BOM, check the Available for all Assemblies box. Clear the box to use only limited assemblies select in the Restrict to Assemblies field.
- To use all locations in BOM check the Available for All Locations box. Clear the box to use only certain locations Select in the Restrict to Locations field.
- If you use one world account Select the Subsidiary.
- Used on Assembly box indicates that BOM is associated to an assembly it means.
- Save.
Create BOM an Assembly item:
- To create new assembly Go to Lists > Accounting > Items.
- In Assembly item page go to manufacturing subtab.
- In the Bill of Materials select New.
- Complete the Bill Of materials & save.
Copying a BOM:
- It is reuse the existing BOM work for create a new BOM.
- Go to List > Supply Chain > Bills Of Materials
- Open the existing BOM record what you want. Open in view mode.
- In actions list, select Make Copy.
- Change the copied BOM name to other.
- Please make the any changes if you want.
- Save.
BOM Revisions:
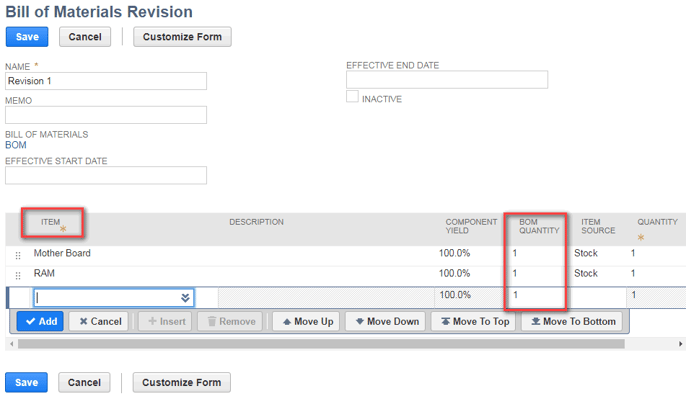
- It is use to update the Bill Of material details of entire product.
- Go to Lists > Supply chain > Bills Of Materials.
- Click view the BOM what you want revise.
- On the Revisions subtab click the Create New Revision.
- Enter BOM name.
- If you want to not appear in search results, check the Inactive Box.
- Select Items what you want include with BOM revision.
- Enter the BOM quantity & select Item source. It means, what item quantity are you taken from like, stock, purchase order.
- Save.
BOM Inquiry:
A BOM Enquiry is used to review the build requirements for an assembly item. It displays how much quantity is there in your assembly components.
- In Administrator account, Go to Transactions > Manufacturing > Bill of Materials Inquiry.
- IF you use one world account select Subsidiary.
- The BOM Inquiry displays Component name, Level, Component yield, Quantity per assembly, on hand qty, Available qty, Backordered, on order.
Finally, It is way of clarifying how to build a product using BOM and instructions for how to assemble the product from the various parts.